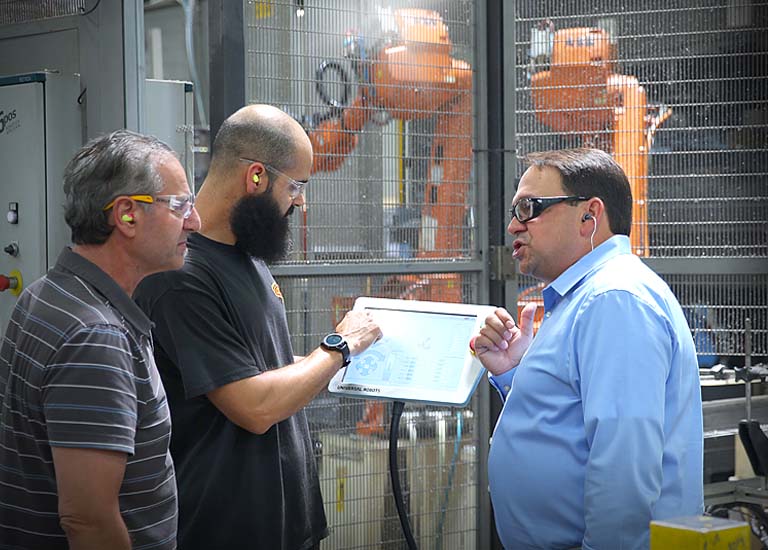
Advanced equipment to advance your business
We have multiple presses that provide the required capacity to serve our growing customer base. Many of our presses—including our 3,300-ton press—feature robotic loading and unloading for high-volume application jobs. We also have presses capable of warm forgings or hot impact extrusions. Our automated processing system cleans and lubricates each steel or aluminum slug prior to pressing.
Utilizing rotary transfer machine technology, we produce parts with extremely tight tolerances at high volume and incorporate visual inspection capabilities.
To ensure we meet the stringent demands of our customers and the industry, we have an on-site quality control lab. Our testing equipment includes a wide array of quality monitoring and testing devices, including coordinating measuring machines, cylinder gauges, height gauges, calipers, and micrometers.