Power of process
Steel impact extrusion creates near-net-shape parts that can lower per-part costs while improving quality. Impacting is often quicker than most other metal-forming processes. Our process is backed by decades of experience and on-site tool and die expertise that can accelerate project timelines while reducing material waste and costs.
Multiple benefits
Reduce per-part costs
Minimize material waste
Strengthen components
Accelerate timelines
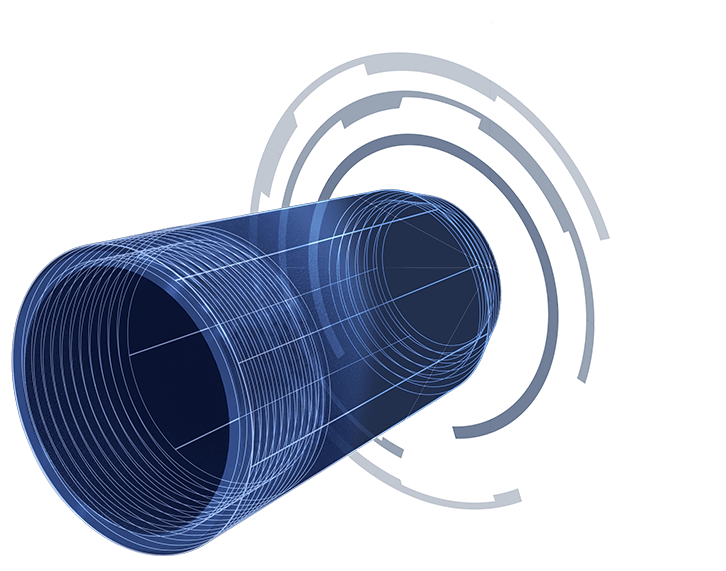